Adsorbents
Durasorb® LNG MAX
Innovative, step-change technology with dual-purpose performance: removal of heavy hydrocarbons and water to cryogenic specifications in a single unit.
This new technology provides a simplified pre-treatment line-up and increases feed gas flexibility. Proprietary adsorbents ensure the removal of trace hydrocarbons, including BTX, which can cause freezing in the coldbox and unplanned plant shutdowns. Durasorb® LNG MAX ensures reliable plant operations and continuous LNG production.
Why BASF?
BASFNatural Gas Treatment experts, positioned around the world, work closely with the customer to provide a tailored solution for the most challenging cases, including heavy gas feeds, gas feeds that contain light mercaptans, and light gas feeds that contain trace heavy hydrocarbons and BTX. Our global network of experts respond quickly to customer inquiries and provide unmatched technical support through the lifetime of the unit.
In 2020, BASF worked closely with Shell to qualify Durasorb® LNG MAX technology. Watch the video to learn more about the technology, the qualification process, and the collaboration.
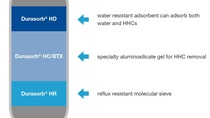
Technology
Leveraging decades of experience designing TSA units for the treatment of natural gas, BASF has developed a multi-layer bed that is resistant to liquid hydrocarbon and water carryover and removes trace heavy hydrocarbons, BTX, and water to cryogenic specifications. With an extensive portfolio of adsorbents at their fingertips, technical experts design the bed to address challenging gas feeds and model all aspects of the adsorption unit to ensure continuous operation for more than 4 years. The newly developed product, Durasorb® BTX, has 30% greater capacity for benzene, toluene, and xylenes compared to other commercially available materials.
Using proprietary modeling tools, BASF technical experts provide unit simulations, including dynamic adsorption and regeneration profiles. This level of detail allows the customer to fully optimize the plant around the adsorption unit, resulting in CapEx and OpEx savings.
Double your impact - Reduce your footprint with Durasorb® LNG MAX
This new technology combines hydrocarbon removal and dehydration into a single unit to provide natural gas that is ready for liquefaction.
With Durasorb® LNG MAX, your business benefits from:
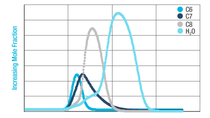
- Unit designs and simulations from best-in-class modeling tools
- Reduced risk of coldbox freezing and unplanned shutdowns
- Increased profit from reliable operations and long life-time warranties
- Increased operational flexibility and ease of adapting to changing feed
gas conditions - Engineering and technical support for smooth project execution and optimized plant performance
Durasorb® LNG MAX is available as a drop-in retrofit solution or to reduce capital expenditure for a new project.
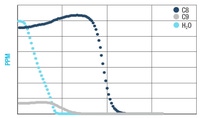
Support and Services
BASF supports its customers in the design and operation of temperature swing adsorption units for gas treatment plants. BASF technical experts provide process design, modeling, and basic engineering. In addition, BASF provides a range of technical services such as debottlenecking and process optimization, troubleshooting and revamps, analytics, and training. BASF tailored solutions address customer specific gas compositions, while considering the CapEx and OpEx priorities of our customers.
BASF delivers:

- Unit Designs and Simulations
- Engineering Services
- Technical Services
- Technology License
- Process Warranty
- Adsorbents
Publications
Results: 9
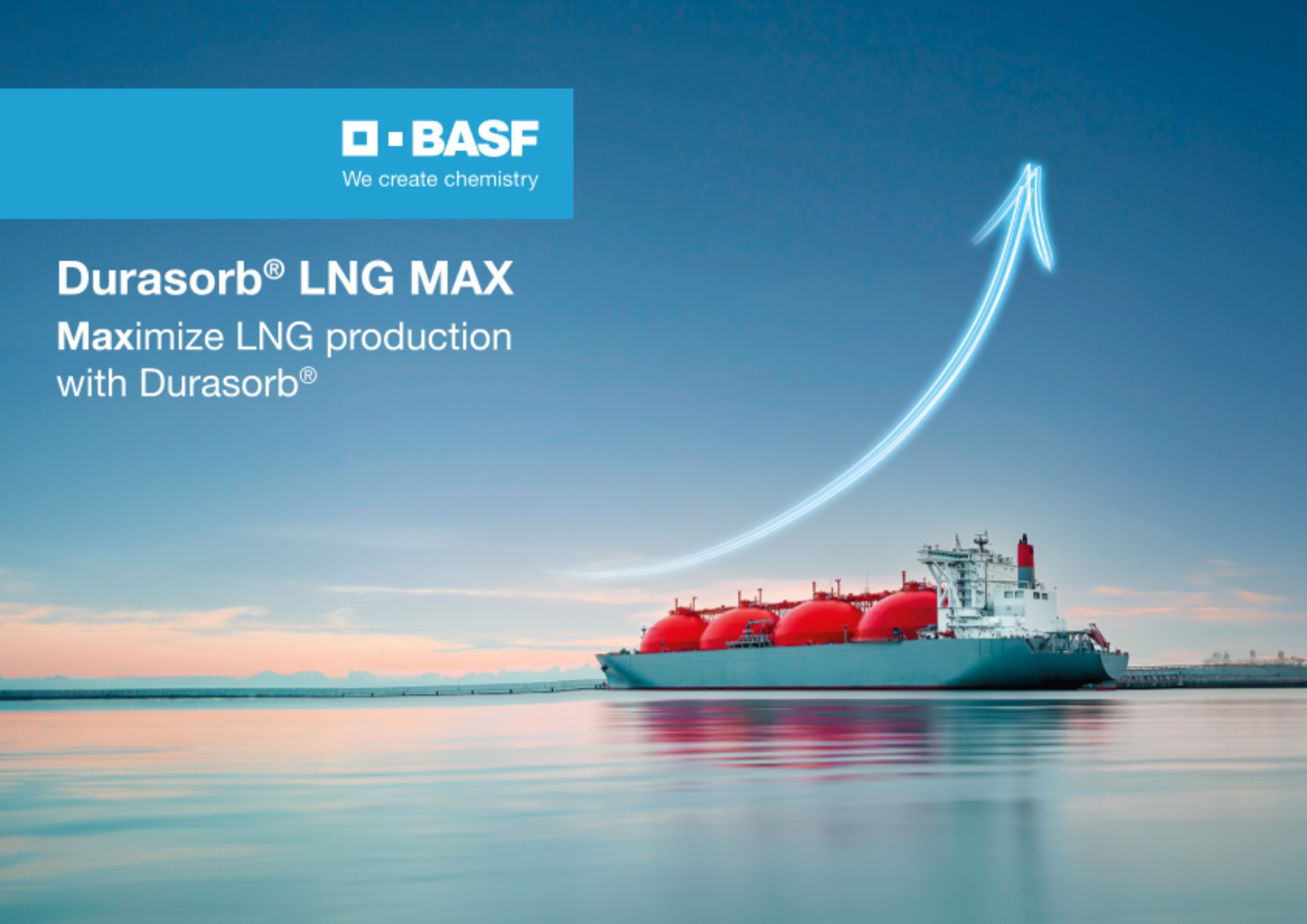
Durasorb for Natural Gas Treatment (Brochure)
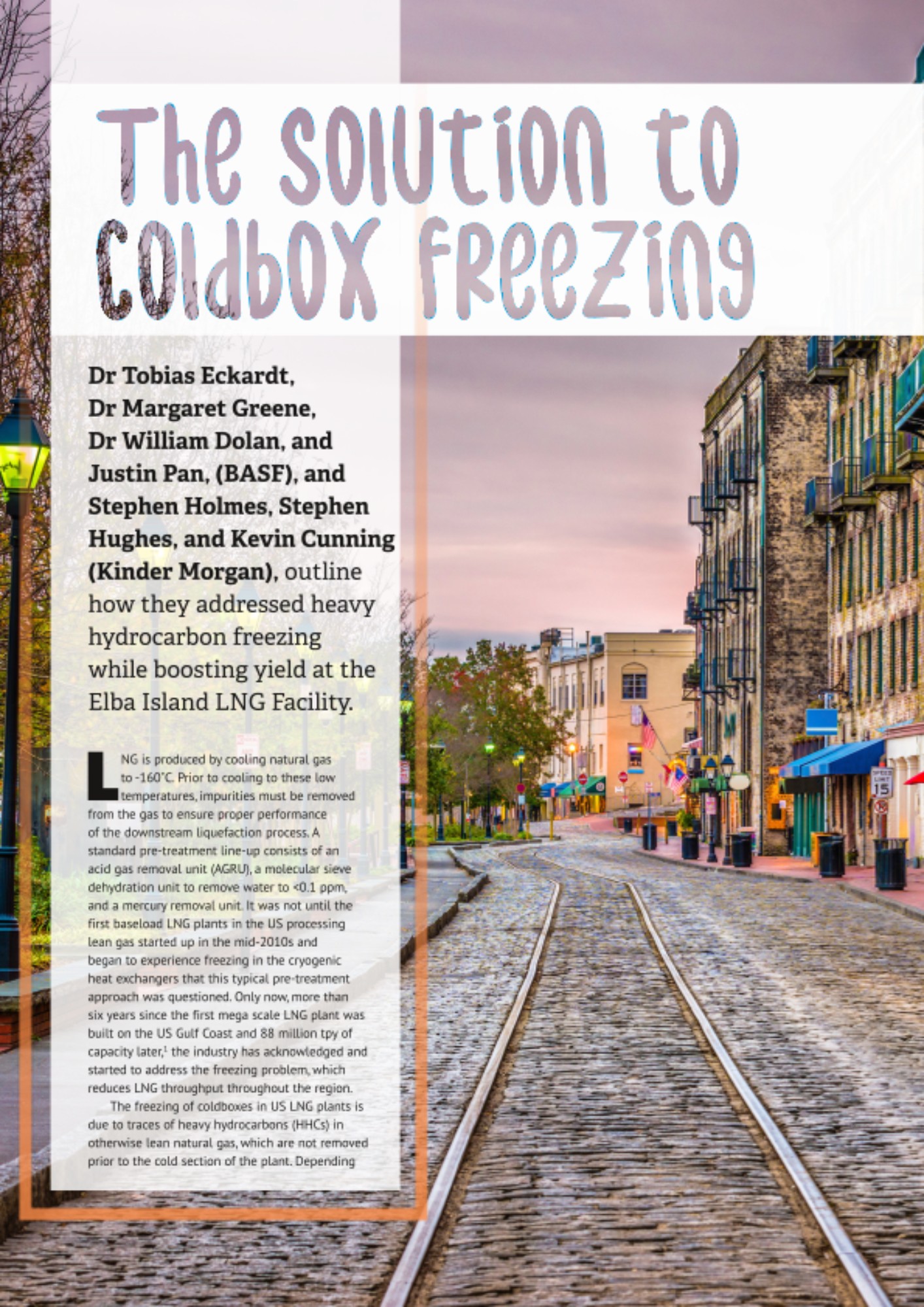
The solution to cold box freezing (LNG Industry Magazine, 2023)
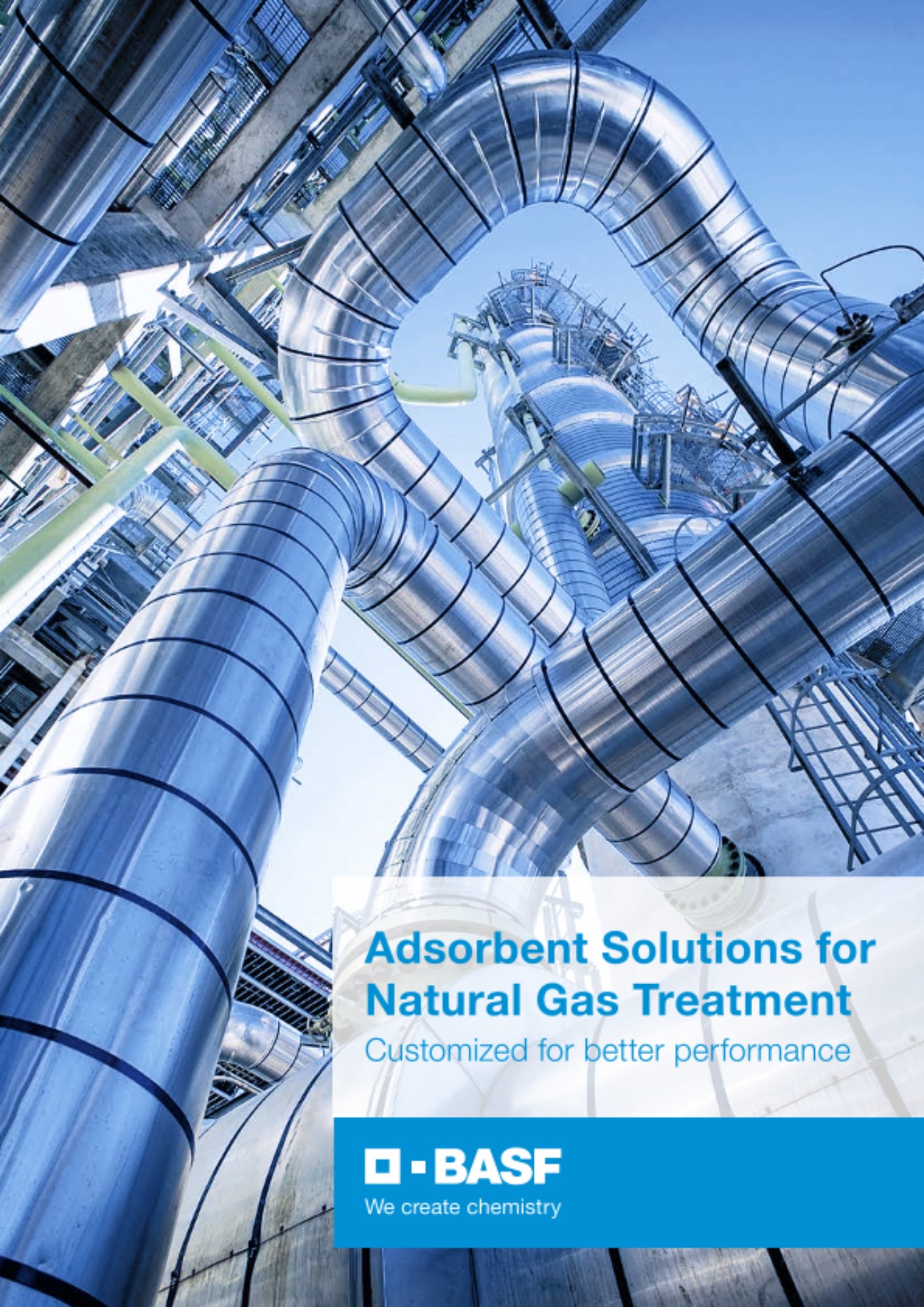
Natural Gas Treatment (Brochure)
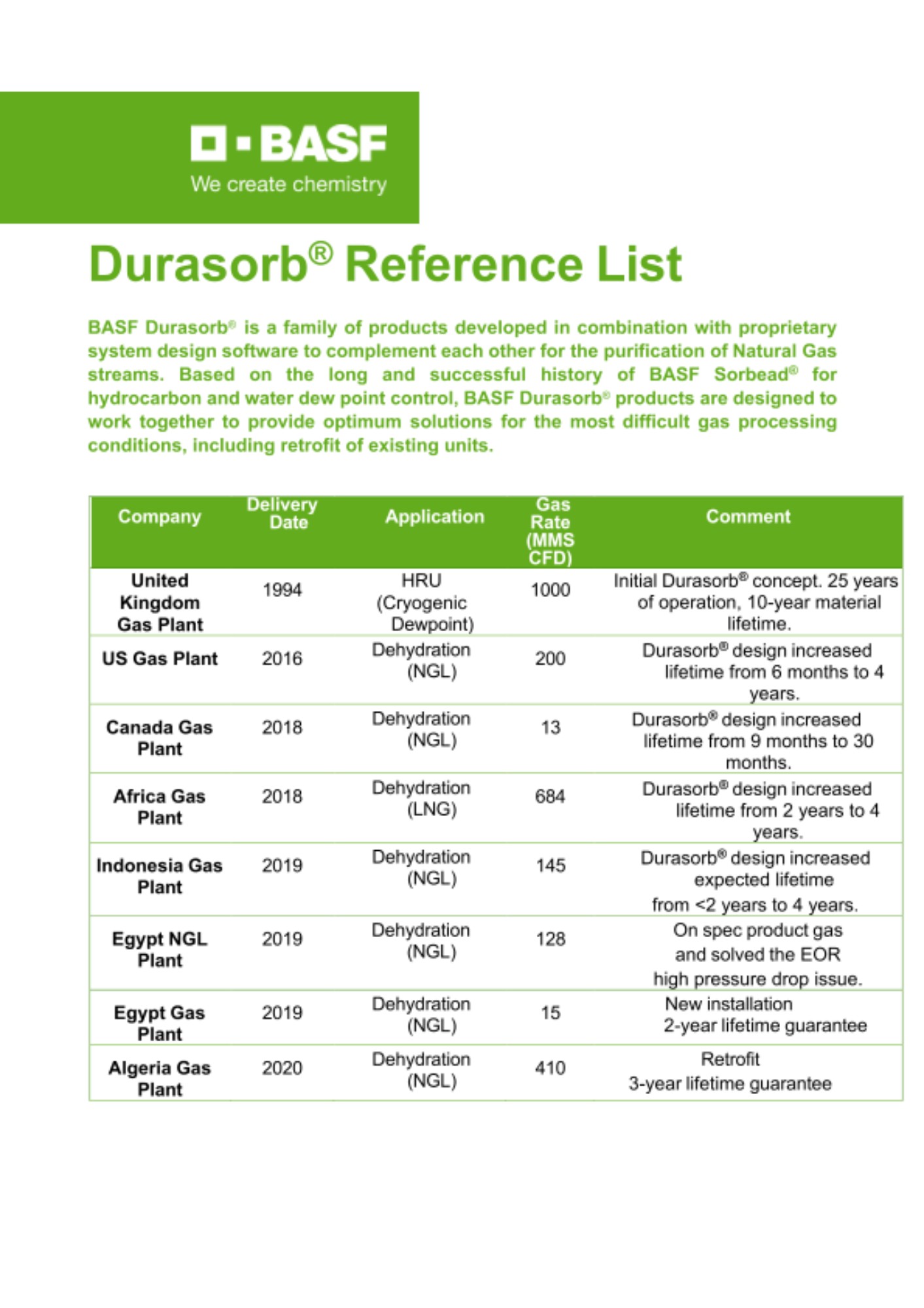
Durasorb® Reference List
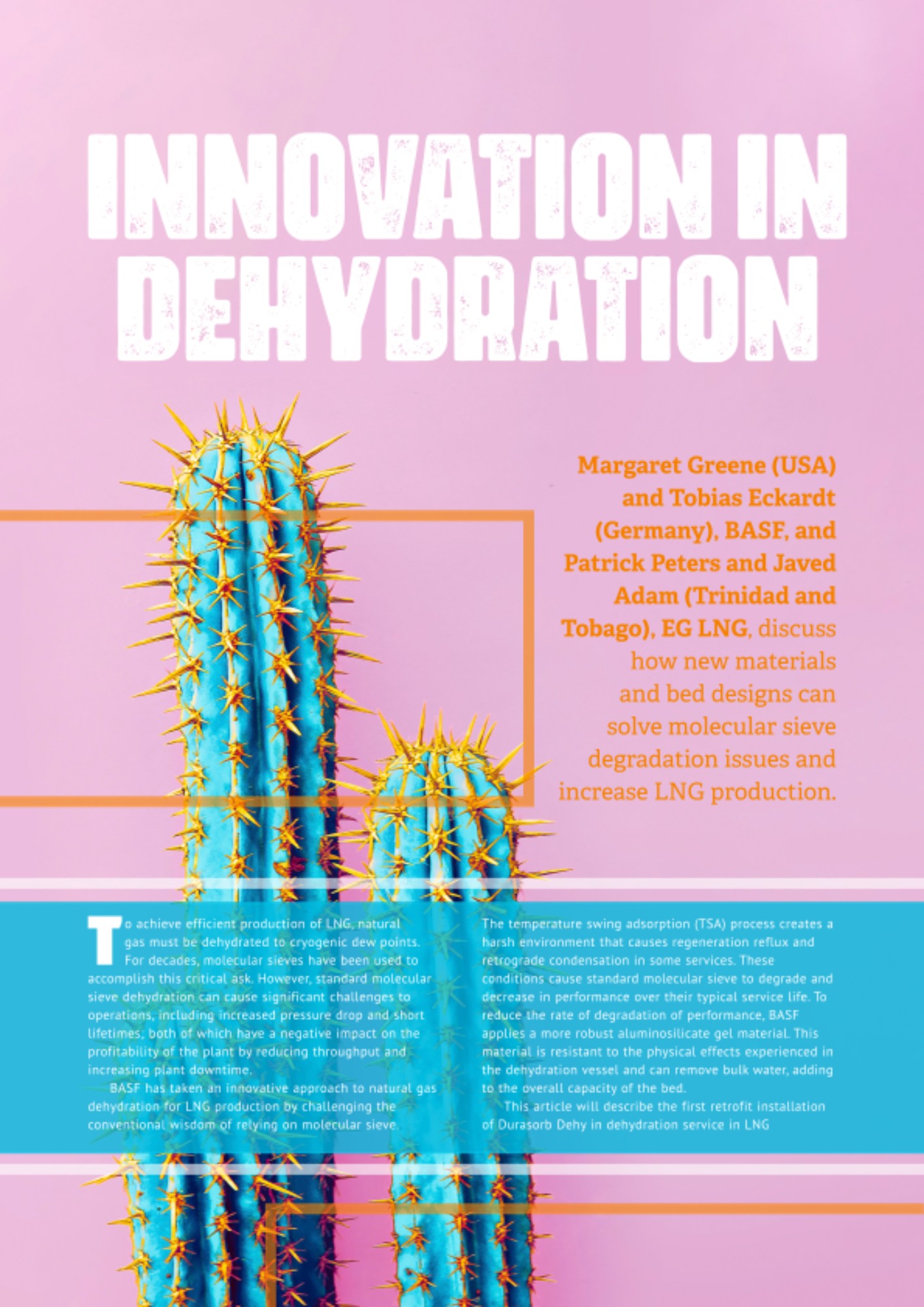
Innovation in Dehydration (LNG Industry Magazine, 2022)
News
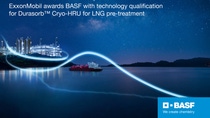
ExxonMobil awards BASF Durasorb™ Cryo-HRU with technology qualification for LNG pre-treatment
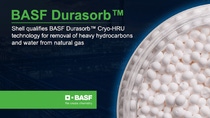